Линия по производству профиля для натяжного потолка. Технология производства натяжных потолков
- Линия по производству профиля для натяжного потолка. Технология производства натяжных потолков
- Бизнес план по производству пвх багета. Оборудование для производства натяжных потолков
- Станок для производства гарпуна. Технология и виды натяжных потолков
- Оборудование для производства багета. Виды оборудования для изготовления багета
- Как изготавливают деревянный багет? С помощью специального оборудования (да, в наше время уже есть даже специальные станки для этой цели)
- Для изготовления багета используется следующее оборудование:
- 1.Скобосшиватель
- 2.Усозарезный станок
- 3.Станок для фрезерования соединений
- 4.Станок для тиснения разделяют:
Линия по производству профиля для натяжного потолка. Технология производства натяжных потолков
Процесс создания подвесных потолков натяжных к особо сложным не относится. Производство полотна для натяжных потолков заключается в как можно более точной выкройке и соединении отдельных полос пленки ПВХ, выпускаемой шириной 1,3 – 1,8 м, в одно целое. На месте соединения полос шва по возможности не должно быть видно.
Для соединения полос пленки любого вида – глянцевой или матовой, чаще всего применяют технологию сваривания токами высокой частоты. Следует отметить, что матовые поверхности свариваются с лучшим результатом монолитности готового полотна. Качество полученного соединения проверяют вручную.
Следующий этап в подготовке полотна – приварка гарпуна, являющаяся ответственной операцией, так как именно она обеспечивает должную степень натяжения потолка.
Технология производства натяжных потолков предусматривает также изготовление специальных профилей. Лучшим по цене сырьем служит крошка пластика (оконный пластик подходит идеально), которую нужно измельчить и при тщательном перемешивании растопить, соблюдая определенный температурный режим и последовательность.
Добавление мела в разумных количествах (около 20%) позволяет удешевить профильное изделие.
Готовая, немного охлажденная масса подается на фильеры, проходя через которые, масса приобретает необходимые очертания профиля. Производство профиля для натяжных потолков завершается нарезкой нужной длины под заказанный размер полотна. Изготавливая профили ПВХ своими силами, можно не только сэкономить средства, но и гарантировать высокое качество своего конечного продукта.
Бизнес план по производству пвх багета. Оборудование для производства натяжных потолков
Для открытия собственного производства натяжных потолков понадобится один или два станка ТВЧ. Стоимость одного станка для сваривания швов и гарпуна составляет от 300 тыс.руб. (однопостовой) до 350 тыс.руб. (двухпостовой). Кроме того, придется приобрести воздушный компрессор (ресивер 50 л) стоимостью до 15 тыс.руб.
Дополнительное электрооборудование (кабель, автоматы и т. д.) обойдется в сумму около 10 тыс.руб. Также для оборудования цеха необходимы один или два стола для раскроя, два стола для подачи материала к станку, упаковочный стол с подогревом, стеллажи для хранения пленки.
На все это придется потратить от 50 до 80 тыс. руб. Кроме того, в бизнес-план надо включить затраты на аренду производственных площадей.
Расходы на дополнительные материалы (металлические уголки, ДСП, подкладочный материал) составят около 5 тыс. руб. Для производства первой партии натяжных потолков понадобятся следующие расходные материалы: пленка ПВХ, багет ПВХ, гарпун, вставка. Не забудьте и про затраты на упаковку (коробки, скотч, воздушно-пузырьковую пленку и т. д.). Минимальная стоимость первой закупки составит 100 тыс.руб.
При подсчетах рентабельности вашего бизнеса по производству натяжных потолков учитывайте, что на изготовление 1000 кв.м потолка (немецкая пленка ПВХ – 60 руб./кв.м) уйдет 1000 пог. м багета ПВХ (22 руб./пог. м), 1000 пог. м вставки (10 руб./пог. м) и 700 пог. м гарпуна (10 руб./пог. м).
Этот расчет дается на производство, в котором будут сочетаться импортная пленка ПВХ и крепеж с багетом российского производства. Однако аналитики прогнозируют, что в ближайшие пару лет модели из российского полотна и фурнитуры, которые полностью соответствуют европейским стандартам качества, вытеснят с рынка «гибридов».
Технология монтажа таких натяжных потолков достаточно проста: по периметру комнаты устанавливается багет (крепежный профиль), на который натягивается ПВХ-пленка.
Существует еще один вид производства потолков – так называемые бесшовные потолки, которые изготавливаются из очень тонкой ткани, пропитанной полимерами с одной или двух сторон.
Розничная цена за один кв. м натяжного потолка российского производства составляет в среднем 400 руб. Квадратный метр натяжного потолка европейского производства обойдется покупателю в 500-900 руб. Потолок премиум-класса стоит от 1500 тыс. руб./кв.м.
Производительность однопостового станка при восьми часовой загруженности в сутки и 22 рабочих днях в месяц составляет 2500 кв. м/мес. Себестоимость одного кв. метра готового потолка составляет 125-200 руб./кв. м.
Если вы планируете не просто организовывать сбыт готовой продукции, но и предоставлять услуги по монтажу, вам понадобится минимум 2-3 бригады по два человека в каждой. При составлении бизнес плана учитывайте расходы на заработную плату монтажникам – от 15 тыс. руб./мес. в расчете на одного человека.
Бизнес по производству натяжных потолков отличается высокой рентабельностью, но не стоит забывать и о высокой конкуренции на этом рынке. Если вам удастся быстро организовать сбыт своей продукции, уже в первые 3-6 месяцев работы вы сможете выйти на уровень самоокупаемости.
Станок для производства гарпуна. Технология и виды натяжных потолков
Процесс изготовления натяжных потолков начинается с такого вещества как поливинилхлорид.
Поливинилхлорид (ПВХ)— это термопластичный материал, который изначально не имеет никакого цвета (по сути — это пластмасса).
Особенность данного материала в наличии таких позитивных характеристик, как:
- стойкость к морозу до -15 градусов;
- не сгорает на открытом воздухе;
- стойкость к нагреванию до +66 градусов;
- устойчивость к щелочам;
- устойчивость к маслам минеральным;
- устойчивость ко многим кислотам;
- устойчивость ко многим растворителям.
Применяется он также в изоляции проводов, в производстве труб, изготовлении искусственной кожи, линолеума, мебельной кромки и т.д. — все это из-за своих качеств.
Недостатком такого материала можно считать лишь то, что при длительном воздействии прямых УФ-лучей он теряет свою эластичность.
Натяжные потолки– это полотнище из того самого материала (ПВХ), которое закреплено на алюминиевом или пластиковом профиле под самим потолком.
Потолок полностью изготавливается под заказ, происходит это методом сваривания поливиниловых полос на производстве, специальными ТВЧ-станками . Ширина одной такой полосы от 1 до 5 метров.
Получившееся полотно разогревается газовыми пушками до температурного значения в 70 градусов по Цельсию, в результате этого оно становится мягким. Такое полотно легко растянуть и смонтировать профиль.
Затем на полотно монтируется гарпун. Он выполняет функцию крепления в профиле.
Формирование гарпуна— не менее важный этап в процессе изготовления полотна, которое в дальнейшем используют для установки натяжного потолка. Данную функцию должен исполнять тот же станок (ТВЧ), что и спаивает полосы ПВХ.
Использование гарпуна при монтаже:
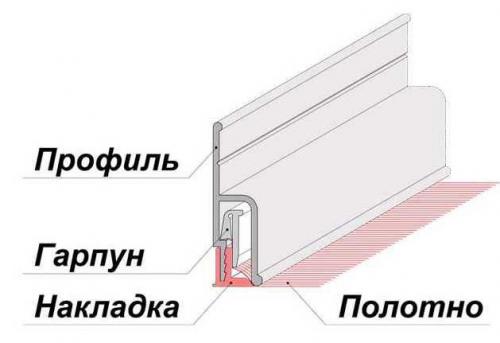
Очевидно, что материал можно заказать в разной цветовой гамме и с разной фактурой.
Чаще всего внимание обращают на такие:
- Глянец— имеет отражающую поверхность, большой выбор в дизайне, легко чистится. Матовый— вписывается в любой дизайн помещения, хорошо передает свой цвет, так как не отражает и не даёт бликования. Сатиновый— очень похож на матовый, тем не менее, благодаря гладкой поверхности, имеет эффект отражения света, что в случае со светлым потолком лишь подчеркивает его яркость и дает небольшой оттенок перламутра.
Оборудование для производства багета. Виды оборудования для изготовления багета
Что такое багет? Французский хлеб? Да, но у слова багет, есть еще другое значение. Багет в столярном мире это профиль, который отделяет картину и интерьера. Виды оборудования для изготовления багета
Ранее, багету, как важной составляющей интерьера внимания практически не уделялось. Со временем дизайнерам удалось доказать, что в интерьере очень большую роль играет так называемая рамка для картины. Багет, в зависимости от его структуры, цвета, фактуры, может сыграть в интерьере очень большую роль. Картина, ее продолжение (багет) и дизайн стены, эти три предмета должны быть максимально гармонично подобраны для достижения цели максимального комфорта глазу.
Как изготавливают деревянный багет? С помощью специального оборудования (да, в наше время уже есть даже специальные станки для этой цели)
Для изготовления багета используется следующее оборудование:
- Скобосшиватель
- Усозарезные станки
- Станок для фрезерования соединений
- Станок для тиснения
- Пресс для сборки багетных рамок
Рассмотрим каждый станок в отдельности, как он работает, какие его виды существуют.
1.Скобосшиватель
Скобосшиватель используется для сборки профиля. Существует пневматический скобосшиватель. Принцип его работы такой же, как у любого бумажного степлера, который мы используем в повседневной жизни. Естественно, сила пневматики у скобосшивателя для багета намного сильнее. Как правила для сшивания профиля багета используются скобы, длиной 8мм; 10мм; 12мм; 15мм. Ширина, как правило, составляет 10мм. Фото степлера для багета представлено ниже.
2.Усозарезный станок
Название станка говорит само за себя: Вырезать усы. То есть это станок, который срезает под углом 45 градусов деревянный профиль багета. Для точной стыковки сторон багетной рамки.
Разделяют :
-автоматические станки двухголовые, предназначены для резки деревянных шипов под углом 45 градусов, деревянного багетного профиля с покрытием ПВХ.
-полуавтоматический станок для резки багетного погонажа
-двухпильный усозарезной станок с максимальным сечение заготовки в 90х88мм
Все станки различаются друг от друга мощностью двигателя двигателя пилы и максимальным сечение обрабатываемых заготовок
3.Станок для фрезерования соединений
Станок используется для фрезерования пазов и отверстий, шиповых соединений
4.Станок для тиснения разделяют:
-Станок для накатки рельефа на пасту
-Станок для горячей накатки рельефа рисунка.